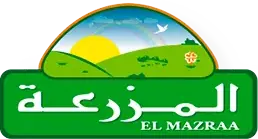
Elmazraa Energy Management
Back to all sucess stories
The Challenge
In 2020, Elmazraa—Tunisia’s largest poultry enterprise—faced a significant challenge. Their by-product processing facility, which transforms chicken waste (carcasses, feathers, blood) into valuable animal feed ingredients, was consuming enormous amounts of energy. The energy-intensive cooking processes, powered by gas-fired boilers and cogeneration systems, were creating substantial operational costs and inefficiencies.
As the central processing hub receiving chicken residues from abattoirs across Tunisia, optimizing this facility’s performance was critical not just for Elmazraa’s bottom line, but for the sustainability of the country’s entire poultry industry.
Our Solution
Intelligent Integration
BIZEYES designed and implemented a comprehensive energy management system that seamlessly integrated multiple data sources:
IoT Network
Deployed throughout the facility to capture real-time environmental and energy consumption data
Production PLCs
Integrated to provide critical production metrics and process parameters
Quality Assurance System
Connected to monitor product quality standards
ERP Integration
Incorporated business data for comprehensive analysis
This unified data ecosystem created a single source of truth for all operational aspects, enabling previously impossible insights into energy usage patterns, production efficiency, and quality control
Smart Technology in Action
The system’s real intelligence came from how it used this integrated data:
Predictive Analytics
patterns of energy consumption to predict and prevent waste
Real-time Monitoring
Provided instant visibility into all cooking processes
Dynamic Alarming
Detected anomalies such as overcooking or excessive energy use as they occurred
Direct Notification
Alerted precisely the right personnel who could take immediate action, bypassing traditional escalation procedures
Continuous Optimization
Automatically adjusted parameters to maintain optimal energy efficiency
Transformative Results
The impact of our system was immediate and substantial
100% ROI Within 12 Months
The entire project investment was recovered in the first year through energy savings alone
Optimized Cooking Cycles
Integrated to provide critical production metrics and process parameters
Enhanced Preventive Maintenance
Decreased equipment downtime through early issue detection
Streamlined Operations
Eliminated bottlenecks in production workflows
Reduced Carbon Footprint
Decreased environmental impact through more efficient energy use
Beyond Energy Savings
While the energy efficiency gains were impressive, the system delivered additional value
Improving Product Quality
More consistent cooking processes led to higher-quality end products
Enhancing Operational Intelligence
Management gained unprecedented visibility into facility operations
Creating a Data-Driven Culture
Staff became empowered to make decisions based on real-time information
Long-Term Impact
Three years after implementation, the system continues to deliver value
- Adapting to changing production requirements
- Identifying new optimization opportunities
- Providing valuable data for strategic business decisions
- Serving as a model for similar implementations across other facilities